NAO, le partenaire qui facilite la relocalisation de la production des petites séries
Ce mois-ci, TEAM Henri-Fabre est partie à la rencontre de jeunes industriels qui souhaitent faciliter la vie de leurs confrères : Gabriel Henry et Pierre Brossier de NAO. Grâce à l’union de leurs compétences, ils ont créé un service clé-en-main qui permet aux industriels de produire des pièces performantes, éco-efficientes, en étant autonomes et rentables, y compris sur de la petite série ou de la pièce unique.
Relocaliser, un casse-tête pour beaucoup de PME industrielles.
Les entreprises qui souhaitent relocaliser leur production, pour des raisons économiques ou écologiques, se heurtent encore à de nombreuses difficultés. La problématique foncière, mais aussi les nécessaires économies d’échelle, le recrutement, tout peut rendre cette opération de bon sens très compliquée !
Les entreprises ont pourtant besoin de produire sur place :
- Lorsqu’elles ont développé un prototype et doivent passer à la production en série,
- Lorsque les besoins sont ponctuels et peu anticipables, voire « à la minute »
- Lorsque les séries sont très petites,
- Lorsque l’on veut maîtriser son concept de A à Z sans communiquer son procédé à un sous-traitant,
- Lorsque tout simplement, on veut éliminer les coûts carbone !
Cette volonté se heurte à des problèmes de faisabilité et de coût. Il faut beaucoup de volonté et une capacité à maîtriser ses prix, ce qui n’est pas toujours possible.
Décarboner et favoriser l’économie circulaire, sans dégrader son fonctionnement ou son EBITDA.
C’est le 2e problème : souvent, la relocalisation se fait pour des raisons écologiques et la crainte est de faire grimper exagérément les coûts de production, sans pouvoir s’y retrouver sur le prix de vente.
Là encore, les problématiques sont nombreuses :
- Les filières de production sont méconnues ou complexes,
- La chaîne logistique peut poser des problèmes,
- Intégrer de nouvelles technologies de production peut être long et difficile,
- La tenue mécanique des matériaux bio-sourcés peut inquiéter.
La solution ? Un centre de production déporté, chez vous, géré par NAO.
Pour répondre à l’ensemble de ces problématiques, NAO propose à ses clients de co-concevoir les pièces et de mettre à disposition un outil de production piloté à distance !
NAO va commencer par sélectionner des matériaux plus écologiques et optimiser le design des pièces à fabriquer, pour concurrencer les matériaux actuels (énergivores et coûteux en transport).
NAO va mettre à disposition une petite unité de production, facile à intégrer dans les locaux du client, y compris en site isolé ! Les centres de production NAO sont compacts et pilotés à distance. Ainsi, l’industriel n’a pas à se soucier de recruter ou former une personne spécifique, ce qui facilite et accélère son projet.
Le coût de fabrication est très compétitif, grâce à un lien entre le design de la pièce, le sourcing des matériaux et la technologie de fabrication. Pour qu’il soit rentable de produire sur place des pièces en petite série à partir de matériaux décarbonés, NAO apporte un savoir-faire unique, qui lui permet de revisiter la conception de la pièce et d’optimiser son coût de fabrication, tout en renforçant la qualité du produit. C’est donc en maîtrisant l’ensemble de la chaîne de valeur que NAO permet à ses clients de produire des pièces techniques, fiables et dans un délai très court.
Et pour les industriels qui souhaiteraient mutualiser un centre de production et encourager l’économie circulaire, c’est également possible !
Les bénéfices pour les industriels ne s’arrêtent pas là…
NAO permet à ses clients de repenser leurs pièces et d’identifier de nouvelles opportunités. Une fois un centre de production installé dans son usine ou son atelier, l’industriel peut faire de la maintenance rapide par exemple, produire son propre outillage… les possibilités sont nombreuses.
Le pilotage à distance de la machine étant entièrement crypté, l’opération est sécurisée. L’entreprise a tous les avantages de la production, sans les inconvénients ! L’industriel dispose de la maîtrise de son outil de production, sans prendre de risque particulier, ni se soucier de la veille technologique ou de la maintenance.
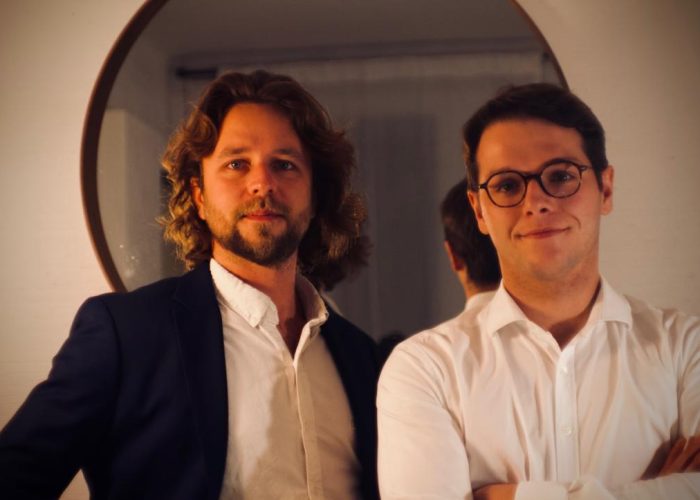
Mais qui sont Pierre et Gabriel, les fondateurs de NAO ?
Ces deux ingénieurs ont fondé NAO il y a moins d’un an. Gabriel Henry est ingénieur mécanique, expérimenté dans le domaine de l’industrie de précision et des énergies renouvelables. Lors de ses précédentes expériences, il a constaté que malgré beaucoup de volonté, les entrepreneurs subissent une « pollution subie » sur certaines pièces qu’ils sont obligés de commander très loin. Il a réalisé aussi combien les petites entreprises peinaient à exister chez leurs sous-traitants quand elles font peu de volume… Et les moyens de production en petite série existent bel et bien, mais ils exigent des compétences spécifiques pour les utiliser, et une capacité d’investissement. C’est ce qui l’a conduit à créer NAO : cette identification de besoins, couplée à son expérience de 10 ans en startup industrielle, autour de la conception, du calcul, prototypage et essais de machines.
Pierre Brossier est Data Scientist Industriel et Docteur en modélisation. Son envie ? Changer la prestation de service de l’ingénierie, pour amener des solutions de manière encore plus simple au client. Sensible à la culture « open source », Pierre rêve de pièces de plus en plus biomimétiques, dont la complexité se rapprochera du vivant. C’est lui le chef d’orchestre de l’éco-conception des pièces, l’expert en design. Depuis 6 ans, il conçoit des modèles et des outils permettant aux ingénieurs d’améliorer leur efficacité.
A eux deux, avec des profils très complémentaires, ils allient une expérience de terrain et des outils informatiques dédiés à l’amélioration de l’ingénierie. Grâce à cette complémentarité, Gabriel et Pierre ont créé avec NAO une innovation de rupture favorisant la relocalisation de la production. Toute la TEAM Henri-Fabre leur souhaite bonne chance et plein de succès dans leur entreprise.